Problems, big and small, are part of everyday life and each of us is used to facing and solving them. The question is: are we all equally effective at solving them?
Many people have a natural ability to solve problems, but this is still a skill that is acquired, in particular, through the application of a method.
“Problem Solving” literally means “problem solving”, that is, the way to give the best possible response to a given critical and unusual situation. In all the problem solving methodologies that can be used (FMEA, 8D, DMAIC,...), the fundamental step that determines the effectiveness of the solution to the problem is the correct analysis of the causes, which in the context of management systems is defined as the “root of cause analysis”.
In 1943, Kuarou Ishikawa, a Japanese chemical engineer and quality theorist, proposed a diagram (both graphical and analytical) for identifying the various causes prior to an event. Also known as a diagram fish bones, or cause-and-effect diagram, it is the most popular tool for the correct execution of root cause analysis.
The Ishikawa diagram is therefore used to define the potential causes of a problem, in order to then implement corrective actions. Its reputation is due to the simplicity with which the tool makes it possible to list all the possible causes of an effect in a systematic and visual way.
It is a tool very often used in brainstorming activities to solve a problem (effect) that is complex in its various factors (causes).
In manufacturing, a particular type of Ishikawa diagram, the 4M diagram, is often used to study problems or processes in the production phase. Compared to an Ishikawa diagram, the categories in which to look for the cause of the studied effect are already defined in the 4M diagram. They are the workforce, the method, the machine, the materials.
Another methodology, complementary to the Ishikawa diagram, to analyze and get to the root of the causes, once identified, is the “5 WHYs” methodology.
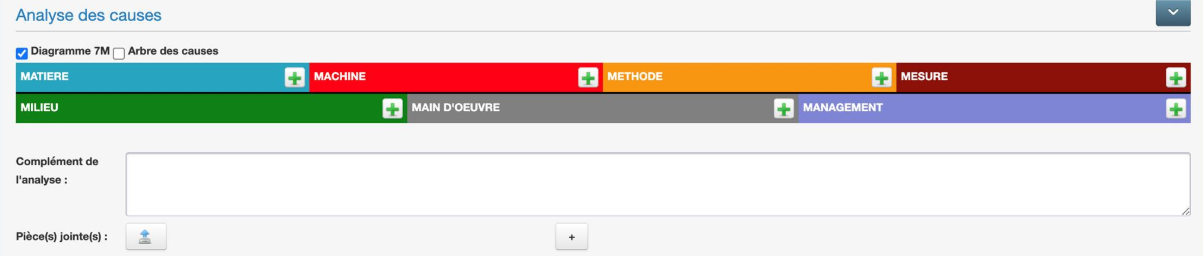