Why make a prevention plan?
The development of a prevention plan should be carried out as soon as there is a coactivity. The simultaneous presence of the staff ofuser company and staff of outside businesses, in the same place, can be a source of risk.
Additional risks may therefore be added to the risks specific to the activity of enterprises, this is explained by the presence of installations, equipment and activities of different enterprises in the same workplace. Working in unknown locations can also worsen and amplify risks.
That is why, the prevention plan is established in cooperation with the companies concerned. It identifies the risks associated with coactivity, thus it makes it possible to foresee the measures necessary for preserve the health and safety of employees.
In the absence of thejoint inspection, of prevention plan and regular meetings during construction, employers are liable to a financial penalty, but also to imprisonment for up to 6 months for involuntary injury.
When should a prevention plan be drawn up?
Before the start of an intervention, the managers of the external company and user must carry out a joint inspection of the workplaces, installations and equipment. This will determine whether the operations to be carried out are likely to create risks and require a prevention plan.
The Labor Code is based on two cases in which a prevention plan must be provided in writing:
- When the number of hours worked is a minimum of 400 hours over 12 months
- When the work to be carried out is on the list of dangerous types of work (included in the order of 19 March 1993 and in the order of 10 May 1994 for agricultural establishments) regardless of the foreseeable duration of the operation.
Preliminary inspection notes the existence of risks associated with coactivity and whether the various conditions are met. Then, the managers of each company are required todevelop a prevention plan jointly, before the start of operations. Otherwise, managers may consider, after analyzing the risks, that the written formalization of a prevention plan is not mandatory. However, it is strongly recommended to draw up a written prevention plan, which includes an analysis of the risks to which employees are exposed.
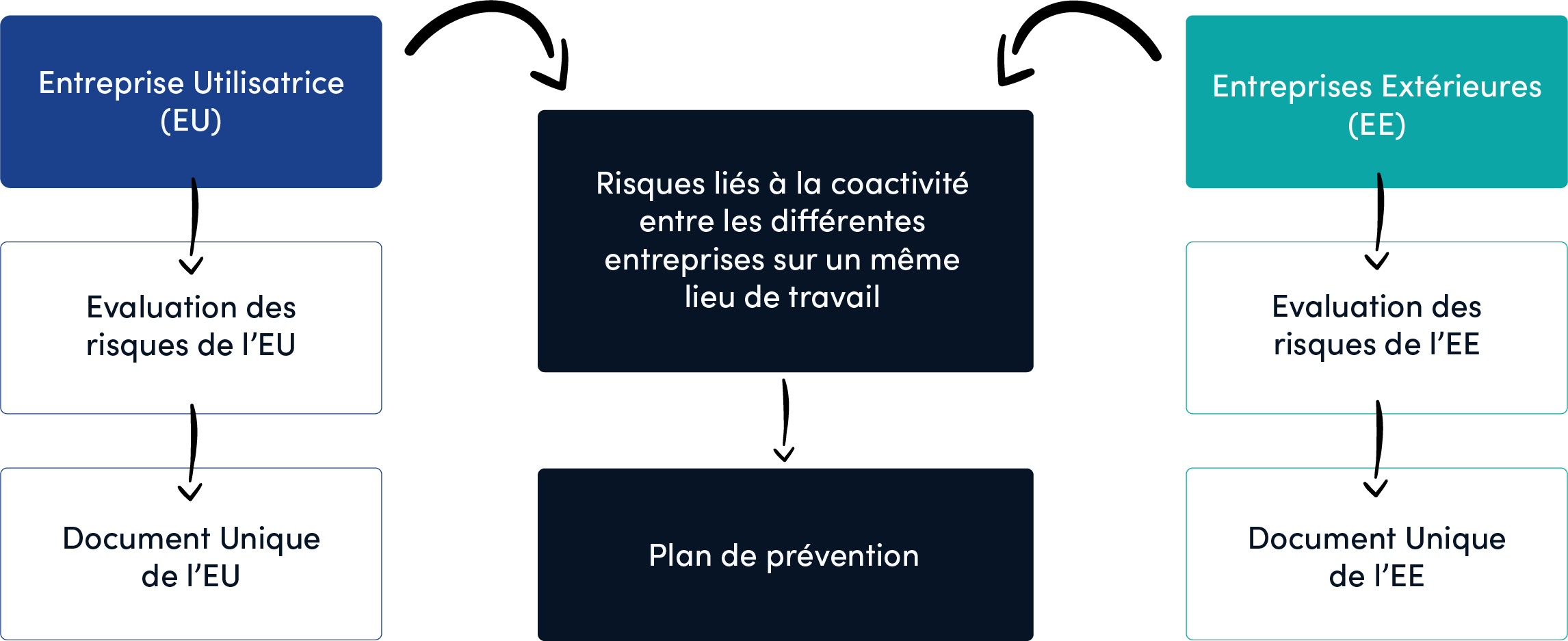
What should you include in a prevention plan?
The prevention plan Provides for various preventive measures, which businesses deem necessary. They may vary depending on the activity, the work to be carried out, the number of companies concerned...
However, the PDP must include the following information:
- The definition of phases of risky activities And Means of prevention correspondents,
- The adaptation of hardware, of installations And devices for the operations to be carried out as well as their maintenance conditions (connection to the network, equipment and work machines, etc.),
- Les instructions to communicate to employees,
- The organization set up for provide first aid in case of emergency,
- La definition of tasks to be performedr, their progression over time, specifying their attribution, the organization of command and the contact details of all the enterprises concerned,
- La distribution of maintenance costs between external companies whose workers use the sanitary facilities, collective changing rooms and catering premises provided by the user company,
- La List of positions in which workers may be subject to increased individual monitoring because of the risks associated with the work carried out in the user enterprise,
- Technical files containing information relating to the research and identification of materials containing asbestos or the asbestos identification report.
Implement your prevention plan:
The prevention plan is signed before the start of operations by the managers of the enterprises concerned or by a person with delegated authority for this action. The employer may delegate an award such as Signature of the PDP, only he can do it to a person who has the necessary authority, competence and means. Then, the manager of the user company checks with the manager of the external company that the measures decided are in place.
Contrary to Single document whose regulations require a review at least every year, no update frequency is provided for the PDP.
So the PDP is valid for the entire duration of the operations. However, companies must ensure that it is updated in order to take account of developments and the real work situation (use of new equipment, intervention of new employees, etc.)
Throughout the duration of the interventions, the PDP must be present at the place where the companies intervene and is available to the following persons:
- Occupational doctors in each company,
- Social and economic committees (CSE) of each company,
- Labour inspection,
- Preventive agents of social security agencies,
- The professional body for the prevention of building and public works (OPPBT), if companies operate in this sector.
In addition, the user company must inform the labour inspectorate in writing of the opening of the works.
How do you save time creating a PDP?
The first change, for simplified creation, is the digitization of your prevention plan.
Going from paper to digital means:
- Be alerted of a document to be updated,
- Have your prevention plans signed electronically and relaunched with a simple click,
- Pre-register your risks and the associated prevention methods.
With our Dyo app, we make that possible. From the planning of external companies to the registration of the Joint Prior Inspection, including the electronic signature, significantly save time for master your prevention plans.
If you want to know more about our solution “prevention plan”, book a free online demonstration, depending on your availability.